In today’s manufacturing world, precision is everything. That’s where CNC machining comes into play. But what is CNC exactly?
CNC, or Computer Numerical Control, is a technology that allows for the automated control of machining tools with incredible accuracy.
This precision machining technique has revolutionized industries, enabling businesses to produce complex parts faster and more efficiently. Curious about how CNC can transform your manufacturing process?
Let’s dive into the 7 powerful benefits of precision machining with CNC technology!
Key Takeaways
- CNC technology automates machining processes, allowing for precise, consistent production with minimal human intervention.
- CNC machining reduces labor costs and waste, enhancing productivity and contributing to sustainability in manufacturing.
- CNC machines are scalable, enabling mass production while maintaining quality and speed, critical for industries like automotive and aerospace.
- CNC machines handle intricate designs that would be difficult or impossible to achieve manually, improving innovation capabilities.
- CNC machining is essential across sectors such as aerospace, medical, automotive, and electronics, ensuring high-quality, durable components.
Table of Contents
What is CNC?
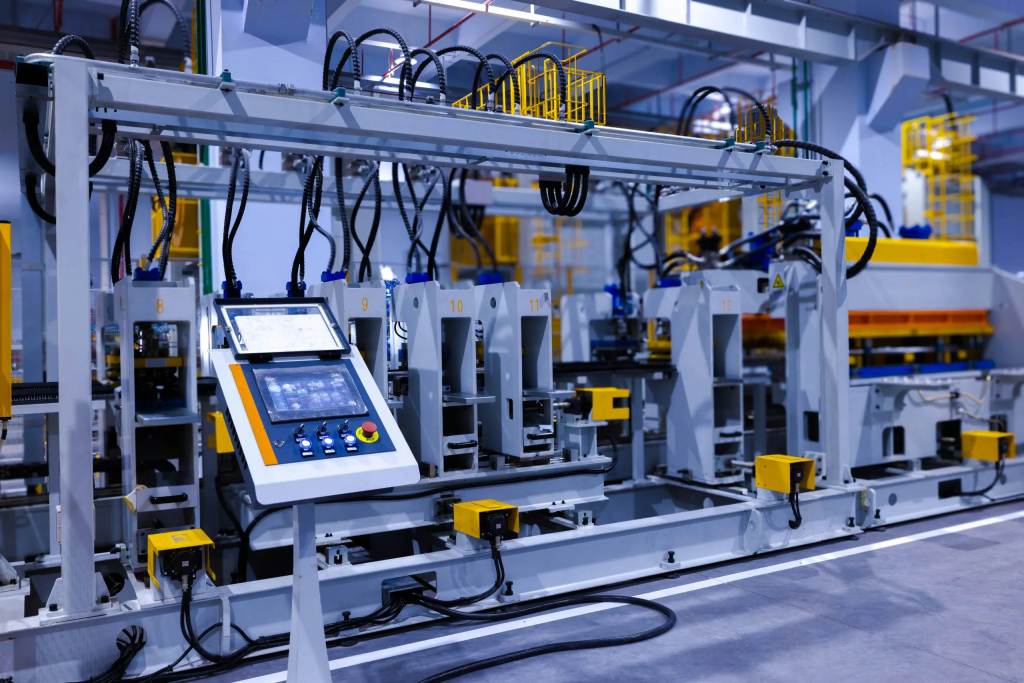
CNC, or Computer Numerical Control, is a manufacturing process that automates the control of machine tools using pre-programmed computer software.
This allows machines like mills, lathes, routers, grinders, and lasers to operate with precision and efficiency, creating high-quality parts without human intervention.
CNC is used in a wide range of industries, including aerospace, automotive, and electronics, to manufacture both metal and plastic parts.
It also controls non-machine tools, such as welding machines, electronic assembly devices, and filament-winding machines, showing its versatility.
History of Computer Numerical Control
Computer Numerical Control (CNC) technology dates back to the 1940s when engineers began experimenting with automating machine tools. Early machines were controlled by punch cards that instructed the tools on how to operate.
In the 1950s, MIT developed the first fully automated CNC machine, using a computer to control tool movement. This was a significant leap from manual operation, drastically improving precision and efficiency.
Throughout the 1960s and 1970s, CNC technology rapidly evolved, integrating more advanced computers and software. This allowed for complex manufacturing processes, which greatly reduced human error.
By the 1980s, CNC machines had become the industry standard for manufacturing. The automation they provided transformed industries like automotive, aerospace, and electronics.
CNC machines have continued to improve with the introduction of microprocessors and CAD/CAM software. These innovations made programming more accessible and enabled even more intricate designs.
In recent years, CNC technology has integrated with AI and IoT, making machines smarter and more adaptive. This development ensures that CNC remains a critical tool for modern manufacturing.
Key Milestones in CNC Evolution
- 1940s: Introduction of automated machine control using punch cards.
- 1950s: MIT develops the first CNC machine controlled by a computer.
- 1960s-1970s: Rapid advancements in computers and software for CNC.
- 1980s: CNC machines become the industry standard in manufacturing.
- 2000s-Present: Integration of AI and IoT to enhance machine performance and adaptability.
CNC has transformed manufacturing and continues to evolve with new technological advancements. Its impact on industries worldwide is undeniable, as it remains essential for precision and efficiency.
What is a CNC Machine and How Does it Work?
A CNC machine, or Computer Numerical Control machine, automates tasks like cutting, milling, and drilling by following computer instructions. It eliminates the need for manual control, allowing for high precision and consistent production.
CNC machines operate using G-code and M-code, programming languages that tell the machine how to move, rotate, and cut materials.
G-code controls the machine’s movements, while M-code handles external functions, such as switching tools or turning the machine on and off.
These machines can work with a variety of materials, including metal, plastic, and wood. They allow for complex designs to be produced accurately, ensuring consistency across mass production.
Each CNC machine has a control unit that processes instructions from the pre-programmed code. This code is generated using CAD software, which converts a digital design into a set of commands the machine can follow.
Once set up, the machine operates with minimal supervision. This increases productivity by allowing continuous, automated production.
CNC machines are essential in industries like aerospace, automotive, and electronics. They make manufacturing faster, more precise, and scalable.
How CNC Machines Operate
- Programming: A design is created using CAD software and converted into G-code and M-code.
- Setup: The material is secured, and the machine is calibrated based on the instructions.
- Execution: The machine follows the G-code to make precise cuts and movements, while M-code manages external functions.
- Completion: The finished part matches the original design exactly.
5 Types of CNC Machines
CNC machines come in different types, each designed for specific tasks in manufacturing.
Let’s discuss five key types of CNC machines and their uses:
1. CNC Milling Machine
CNC milling machines use rotating cutting tools to shape materials like metal and plastic. They are commonly used for complex parts in industries such as aerospace and automotive.
2. CNC Plasma Cutters
CNC plasma cutters use a plasma torch to cut conductive materials like steel. These machines are known for their speed and precision, often used in shipbuilding and metal fabrication.
3. CNC Lathe Machines
CNC lathe machines rotate the material while cutting tools shape it. They are ideal for creating cylindrical parts, widely used in metalworking and woodworking.
4. CNC Laser Cutting Machines
CNC laser cutting machines use a high-powered laser to cut or engrave materials like metal and wood. They are perfect for industries requiring intricate designs, such as electronics and jewelry.
5. CNC Drilling Machine
CNC drilling machines automate the drilling process, creating precise holes in various materials. They are essential for industries like electronics and automotive, where accuracy is critical.
7 Importance of CNC Machining
CNC machining plays a critical role in modern manufacturing, offering numerous benefits that streamline production and enhance efficiency.
Here are the seven key reasons why CNC machining is essential:
Importance | Description |
---|---|
Cost Reduction | Automates tasks, lowering labor and production costs. |
Waste Reduction | Precise material control reduces waste and supports sustainability. |
Human Error Reduction | Automation ensures consistent accuracy and reliability. |
Contour Machining | Handles complex designs with high precision. |
Faster MCU Programming | Quicker setup times boost productivity. |
Improved Operational Intelligence | Provides real-time data for better decision-making. |
No Bottlenecks | Continuous operation minimizes production delays. |
1. Cost Reduction
CNC machining reduces labor costs by automating tasks that would otherwise require multiple operators. This leads to lower production costs and more efficient resource utilization.
2. Waste Reduction
By using precise cutting and material control, CNC machining minimizes waste during the manufacturing process. This reduces raw material costs and contributes to sustainability efforts.
3. Human Error Reduction
Automation in CNC machines eliminates the risk of human error, ensuring that parts are produced with consistent accuracy. This increases reliability and lowers the chances of defects.
4. Contour Machining
CNC machines can handle complex contour machining that would be difficult to achieve manually. This capability allows manufacturers to create intricate designs with high precision.
5. Faster MCU Programming
CNC machining allows faster programming of the machine control unit (MCU), leading to quicker setup times. This boosts productivity and shortens the overall production cycle.
6. Improved Operational Intelligence
CNC machines provide real-time data on machine performance and operations. This helps manufacturers make informed decisions to optimize production and maintain efficiency.
7. No Bottlenecks
With CNC machining, production bottlenecks are minimized as the machines can run continuously with minimal supervision. This ensures a smoother and faster production process.
CNC Important Applications
CNC machining is critical across industries, offering precision, efficiency, and reliability. It’s a vital tool for manufacturing complex and high-quality components.
Aerospace
CNC machining ensures precise production of critical aerospace parts like turbine blades and landing gear. The technology handles materials such as aluminum and titanium, meeting strict tolerance standards for safety and performance.
Key components:
- Landing gear
- Airfoils
- Engine parts
- Manifolds
Medical Equipment
In the medical field, CNC machining produces surgical instruments and implants with high precision. It ensures biocompatibility and fast production of essential devices, especially during high-demand periods like the COVID-19 pandemic.
Typical products:
- Surgical instruments
- Implants
- Orthotic devices
- Monitoring device enclosures
Automotive
CNC machining is used for producing durable engine parts, gears, and axles. Its precision enhances vehicle safety and performance, whether in prototyping or mass production.
Key components:
- Gearboxes
- Engine parts
- Cylinder blocks
- Dashboard panels
Electronics
CNC machining enables the precise production of electronic components such as printed circuit boards and heat sinks. It works with metals, plastics, and ceramics, streamlining the production process.
Common components:
- Printed circuit boards
- Heat sinks
- Electrical insulation
- Device housings
Oil and Gas
CNC machining manufactures durable equipment like valves and pumps for the oil and gas sector. These parts withstand extreme conditions and ensure operational efficiency.
Key components:
- Drill bits
- Pistons
- Valves
- Hydraulic systems
Marine
In marine applications, CNC machining produces reliable parts such as propellers and engine components. These parts, made from corrosion-resistant materials, perform well in harsh environments.
Marine components:
- Propellers
- Engine parts
- Hull fittings
- Prototype molds
What is a CNC Machinist and How to Launch a Career as a CNC Machinist?
A CNC machinist is a skilled professional responsible for operating and programming CNC (Computer Numerical Control) machines.
These machines are used to manufacture precision parts from materials like metal, plastic, and wood in industries such as aerospace, automotive, and medical.
Responsibilities of a CNC Machinist
CNC machinists set up machines, choose the correct tools, and program them to follow specific designs. They monitor the machines throughout production, making adjustments as needed to ensure accuracy and efficiency.
Skills and Qualifications
CNC machinists must read blueprints, interpret technical drawings, and use CAD software. Strong problem-solving abilities and attention to detail are crucial to maintaining quality and meeting design specifications.
Why CNC Machinists are Important
CNC machinists are essential to modern manufacturing, providing the precision required for high-quality parts. Their expertise ensures products are made efficiently, reducing errors and production costs.
Tools and Equipment
CNC machinists work with advanced machinery, including CNC lathes, mills, and routers. These machines allow them to produce intricate designs with high precision, making them key players in high-tech manufacturing.
How to Launch a Career as a CNC Machinist
To become a CNC machinist, you’ll need vocational training or an apprenticeship. Many employers prefer candidates with certifications, such as those from the National Institute for Metalworking Skills (NIMS), which demonstrate proficiency.
Building Experience
Start by learning basic machining skills, then gradually work toward more complex tasks. Hands-on experience through internships or entry-level positions will provide the foundation needed for success in this field.
Career Advancement Opportunities
With experience, CNC machinists can advance to roles such as CNC programmers or supervisors. Continuing education and certifications can help you stay competitive and move up the career ladder.
Conclusion
CNC machining is a game-changer for modern manufacturing, offering precision, efficiency, and flexibility. By automating complex processes, CNC helps industries produce high-quality parts faster and more cost-effectively.
Whether you’re aiming to reduce waste, improve accuracy, or scale production, CNC technology provides powerful benefits that enhance operational success.
Embracing CNC means staying competitive in industries like aerospace, automotive, and electronics.
Ready to leverage the advantages of CNC in your manufacturing process? Start exploring how this technology can transform your business today.
Let’s continue the conversation and unlock even more possibilities with CNC precision machining!
Ready to Boost Precision in Your Manufacturing?
Discover more insights in our TMGVoice blogs on CNC and precision machining, and explore TMGVoice.com to learn how our solutions can enhance your production.
Start improving your process today!
FAQ
How Does CNC Machining Improve Production Efficiency?
CNC machining improves efficiency by automating processes, reducing errors, and enabling faster production cycles.
What Industries Commonly Use CNC Precision Machining?
Industries such as aerospace, automotive, electronics, and medical commonly use CNC precision machining.
How Does CNC Technology Ensure Consistent Quality in Manufacturing?
CNC technology ensures consistent quality by using programmed instructions that produce precise and repeatable results.
What are the Maintenance Requirements for CNC Machines?
Maintenance includes regular cleaning, lubrication, inspection of parts, and software updates to ensure optimal performance.