Imagine a world where every process is almost perfect. In this world, efficiency is a constant reality, not just a goal. Feedback loops in closed-loop systems help cut errors by up to 60%. This shows how powerful this technology is.
In a field where accuracy matters most, the closed-loop system is a top example of automatic control innovation. This engineering marvel not only makes processes automatic. It also corrects and regulates itself impressively.
In this article, we will discuss what closed-loop systems are, how they work, how they compare against an open-loop control system, and many more.
Let’s get right into it.
Key Takeaways
- Feedback loops are crucial for enhancing precision and efficiency in closed-loop systems, reducing errors significantly.
- Closed-loop control systems autonomously minimize errors and maintain high levels of process control, ensuring consistent performance.
- Fully automatic control systems offer significant advantages across various industry sectors, improving reliability and efficiency.
- Implementing successful closed-loop systems requires careful consideration of critical components and steps, ensuring effectiveness in operations.
- Sophisticated closed-loop control systems have a substantial impact on overall productivity and error reduction, optimizing performance in complex settings.
Table of Contents
What is a Closed Loop Control System?
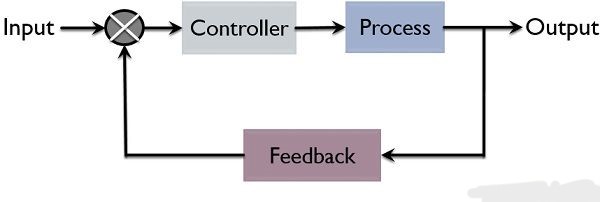
A closed-loop control system is an automated system designed to regulate processes precisely and maintain a desired state or set point without human intervention. Its key feature is a feedback mechanism that continuously adjusts the control signal based on an error signal, ensuring the system output aligns with the target.
Thanks to its dynamic nature, your processes adapt well to changes. This maintains top performance and consistency. A closed-loop control system is a smart choice for improving reliability and efficiency in complex settings.
Why Is a Closed-Loop System Important?
In industrial settings, control systems play a crucial role in keeping things running smoothly. A closed-loop system, or feedback controller, makes ongoing adjustments to stick to desired output conditions. It does this with little need for people to step in. This approach uses system parameters and control moves for steady performance.
At its core, a closed-loop system in industrial uses can make control actions on its own, based on the latest data. This self-fixing feature keeps processes in line with their goals. But why are these systems so essential?
- Improves Process Reliability
- Enhances Efficiency
- Reduces Error Margins
- Optimizes Production
Here’s a closer look:
Aspect of Closed-Loop System | Benefits in Industrial Applications | Considerations for System Parameters |
---|---|---|
Self-regulation | Adjusts processes in real-time to avoid deviations from set standards. | Parameters must accurately represent process conditions to inform appropriate control actions. |
Precision Control | Targets precise outcomes, reducing waste and enhancing product quality. | Control algorithms need calibration to match the dynamic nature of the industrial environment. |
Adaptability | Flexible to changes in operational conditions or objectives. | Feedback mechanisms must be responsive to fluctuating operating variables. |
Reduces Human Error | Limits the scope for human oversight by automating control decisions. | Training of personnel to understand system reports and alerts is necessary. |
Cost Efficiency | Decreases operating costs by preventing resource overuse and downtime. | Must accommodate cost-effective maintenance without compromising on quality or performance. |
7 Real-Life Examples of Automated Closed-Loop Systems
Imagine a world where tech takes care of your comfort and safety. In this world, automated closed-loop systems handle everything smoothly. They use self-regulating mechanisms to achieve a desired response. These systems range from simple household gadgets to complex nuclear power plants.
System | Function | Key Component |
---|---|---|
Thermostat Control System | Keeps vehicle at a steady speed | Temperature Sensor |
Cruise Control in Automobiles | Keeps vehicle at steady speed | Speed Sensor |
Automatic Water Level Control | Ensures consistent water level in tanks | Water Level Sensor |
Aircraft Autopilot Systems | Automatically navigates aircraft | Gyroscopes and GPS |
Home Lighting Systems | Adjusts lighting based on conditions | Light and Motion Sensors |
Water Level Control in Tanks | Stabilizes residential water supply | Pressure Sensors |
Satellite Attitude Control | Maintains satellite orientation | Star Trackers and Sun Sensors |
1. Thermostat Control System
At home, a thermostat keeps your place just how you like it. It uses a temperature sensor to adjust the heat or AC. This way, it matches your process variable or the temperature you’ve set.
2. Cruise Control in Automobiles
When you drive cruise control helps keep your car moving steadily. It uses feedback loops to change speed based on your settings and the road.
3. Automatic Water Level Control in Tanks
In big industries, water level control is key. Systems ensure a stable water level using sensors. They turn pumps and valves on or off based on needs.
4. Aircraft Autopilot Systems
Think of the autopilot in an airplane. It combines sensors and algorithms to guide the plane. This happens without the pilot having to do much.
5. Home Lighting Systems
Your home lights can adjust themselves too. They sense if someone is in the room and how much light is needed. This saves energy while giving you the best light.
6. Water Level Control in Tanks
At home, water systems also use sensors. They make sure you always have enough water pressure for a shower.
7. Satellite Attitude Control
Out in space, satellites need to be positioned right. Their control systems help them stay aligned. This is vital for good communication and data.
9 Steps on How to Get Started with a Closed-Loop System
Starting a closed-loop feedback system enhances your work and keeps quality steady. It needs careful planning and smart actions. These steps guide you through it easily.
Step Number | Action |
---|---|
1 | Define System Objectives |
2 | Select Sensors and Actuators |
3 | Design Control Algorithm |
4 | Implement Hardware and Software |
5 | Test and Validate |
6 | Fine-Tune Parameters |
7 | Monitor and Maintain |
8 | Empower Your Employees |
9 | Iterate and Improve |
1. Define System Objectives
Start by pinpointing what you want to achieve. It might be a set speed in production or a precise temperature in a greenhouse. Knowing your goal directs your control loop’s setup.
2. Select Sensors and Actuators
Pick sensors and actuators that read and act on system changes well. Good parts make a feedback system that adjusts reliably based on control signals.
3. Design Control Algorithm
Your algorithm is your operation’s brain. Design it to handle the control signal and give commands to keep things within range. A strong design ensures a stable control loop.
4. Implement Hardware and Software
Set up your sensors, actuators, and computers, then add your control software. Merging these components forms your closed-loop feedback system’s core.
5. Test and Validate
Testing checks if everything works as one, spotting any performance gaps. This step confirms your system is ready and meets all needs before its actual launch.
6. Fine-Tune Parameters
Tuning your system is an art. Change and test repeatedly to refine the feedback control. This makes sure it hits your control action standards.
7. Monitor and Maintain
Stay alert to keep your system accurate and reliable. Checking and maintaining your setup helps avoid issues and keeps everything working as it should.
8. Empower Your Employees
Teach your team how to use the new system. Educated staff can keep things running right and adapt to any control signal changes.
9. Iterate and Improve
Keep aiming to do better. Making small, ongoing improvements allows your closed-loop system to adapt and stay modern.
10 Components of Closed Loop Control System
It’s important to grasp how a closed-loop control system works to make it better. Each part, like sensors and actuators, links together to boost efficiency. This system adjusts constantly to ensure actions match goals accurately. Let’s look at each piece and its job within the system.
Component | Function | Role in Feedback Loop |
---|---|---|
Controller | Processes input signals and commands actuators | Brain of the operation, decision-making based on feedback |
Actuators | Executes commands from the controller | Physical enforcer of the control output |
Sensors | Monitors system performance | Gathers data for feedback signals |
Process or Plant | Where the actual system change happens | The brain of the operation, decision-making based on feedback |
Reference Input/Setpoint | Defines what the system should achieve | The objective or goal for system output |
Feedback Path | Channels feedback signals to the controller | Ensures a closed loop by returning sensor data |
Control Algorithm | Determines system response to deviations | Dictates how controller output is calculated |
Error Detector | Identifies discrepancies between actual and desired outputs | Initiates correctional measures |
Controlled Output | The subject of control actions | Depicts the efficacy of the feedback system |
Setpoint | Target value for the system | Performance benchmark within the feedback loop |
1. Controller
The controller is the system’s brain. It takes in signals and decides how to act to meet the goal. It keeps the system stable by processing feedback.
2. Actuators
Actuators make the controller’s decisions happen. They change controller orders into real actions. This makes them key in the feedback loop.
3. Sensors
Sensors are vital as they collect real-time data. This data tells the system how close it is to reaching its goal. It then uses this info to adjust.
4. Process or Plant
The process or plant is where the action happens. It reacts to actuator changes. This keeps the feedback cycle moving.
5. Reference Input
The reference input is your goal. It’s what the controller aims for correct errors and make adjustments.
6. Feedback Control System
The feedback path brings sensor data back to the controller. It’s crucial for comparing results to the goal.
7. Control Algorithm
This sets the rules for turning errors into actions. It’s key to getting the desired results in the system.
8. Error Detector
The error detector spots differences between reality and goals. Spotting these differences is key for making corrections.
9. Controlled Output
This shows how well the system is doing. It reflects the actuator’s changes and if the set point is met.
10. Setpoint
The set point is the target the system works towards. It’s the standard for measuring the system’s success in the feedback loop.
Advantages and Disadvantages of Closed Loop Systems
Aspect | Advantages | Disadvantages |
---|---|---|
Accuracy | Provides precise control over system variables, leading to accurate outputs. | Dependence on accurate sensors and actuators; the system may still experience errors if these components fail. |
Stability | Ensures system stability by continuously adjusting to maintain set parameters. | Complexity in tuning parameters may be required to achieve the desired accuracy. |
Efficiency | Optimizes system performance by reducing errors and minimizing energy consumption. | Initial setup and tuning can be time-consuming and resource-intensive. |
Adaptability | Can adapt to changes in operating conditions or disturbances, maintaining desired outcomes. | Complexity in design and implementation may hinder rapid adaptation to new requirements. |
Error Reduction | Minimizes errors and deviations from setpoints through continuous feedback adjustments. | Dependence on accurate sensors and actuators; system may still experience errors if these components fail. |
Robustness | Offers robust performance in the face of external disturbances or variations. | Complexity increases vulnerability to malfunctions or errors if not properly maintained or monitored. |
Reliability | Provides reliable operation over extended periods, ensuring consistent performance. | Relies on proper maintenance and periodic calibration to prevent drift or degradation over time. |
Types of Feedback in Closed Loop Systems
In closed-loop systems, feedback is key to how well things work. Positive and negative feedback are two types that change how controls work. We will look at how they affect signals and control loops.
Positive Feedback
Positive feedback makes system changes bigger, on purpose. It boosts a certain action or result. This feedback isn’t used much in controls, but it’s important for some jobs. It can move a process to a new state, acting as a switch within the system limits. Positive feedback is key when quick changes are needed.
Negative Feedback
Negative feedback is a big part of most control systems. It helps match the actual results to what’s wanted. It uses feedback signals that are opposite to the error. This makes the system stable and keeps the outcomes close to the goal. This kind of feedback helps keep things balanced in complex situations.
Closed Loop vs. Open Loop Systems
Aspect | Closed Loop Systems | Open Loop Systems |
---|---|---|
Feedback | Utilizes feedback mechanisms to adjust system behavior based on measured output. | Does not incorporate feedback; operates without adjustments based on output. |
Control | Offers precise control over system variables. | It does not incorporate feedback and operates without adjustments based on output. |
Accuracy | Tends to be more accurate due to continuous adjustments. | May be less accurate as it doesn’t account for variations or disturbances. |
Stability | Generally more stable due to continuous feedback control. | May experience stability issues, especially with external disturbances. |
Adaptability | Can adapt to changes in operating conditions. | Less adaptable; fixed control settings may not accommodate variations. |
Error Reduction | Minimizes errors through feedback-driven adjustments. | Errors may occur and persist without feedback-driven corrections. |
Complexity | Often more complex due to feedback loop implementation. | Typically simpler in design and implementation. |
Reliability | Generally reliable, provided feedback loop is well-designed and maintained. | Reliability may vary depending on system robustness and external factors. |
Conclusion
Closed loop systems play a critical role in precise control over different processes. They help achieve a specific state automatically. This is crucial in things like cruise control to keep the car moving at the right speed.
The feedback loop in these systems makes sure there’s a close match between output and value. When there’s a deviation, it’s quickly corrected. This results in nearly zero error during operation.
Closed-loop systems are far more efficient than open-loop ones, especially when mistakes can’t be tolerated. They adjust outputs in real time to match changes. This flexibility is key in industries like automotive and aerospace for flawless operation.
At their core, closed-loop control systems are vital for automation and precision engineering. They consider real-time outputs to ensure stability and performance. As technology grows, these systems become more sophisticated.
This growth leads to better automatic performance with less need for people to step in. With ongoing improvements, closed-loop systems are set to explore new areas. They’ll keep pushing innovation forward.
Author’s Bio:
Scott McAuley is the CEO of TMG Voice. Great teamwork starts with TMG Voice, where all your people, tools, and communication come together for faster and more flexible work.
We offer unparalleled phone service with EPIC support from real humans, no long-term contracts, and the lowest prices with the greatest features. Experience seamless, cost-effective, and personalized telecommunications solutions tailored to your business’s unique needs.
For more information about TMG Voice’s Business Communication services, visit our Plans and Pricing page or contact us using our hotline (832) 862-6900. You can also visit our office at 21175 Tomball Parkway #361 Houston, Texas 77070, or send a message to our email through our Contact Us page.
Achieve Closed-Loop System Success With Expert Insights
Ready to optimize your processes? Explore our blogs for in-depth guidance on closed-loop strategies, and visit TMGVoice for solutions designed to streamline your operations.
Start implementing efficient workflows today!
FAQ
What is a Closed-Looped System?
A closed-loop system, also known as a feedback control system, uses feedback from its output to regulate or adjust its operation, maintaining desired conditions or performance.
What is an Open-Loop vs a Closed-Loop System?
In an open-loop system, there is no feedback mechanism, so the output is not adjusted based on input. In a closed-loop system, feedback is used to adjust the system’s operation.
What is the Meaning of a Closed-Loop System?
A closed-loop refers to a system where the output affects the input, creating a feedback loop that allows the system to regulate itself and maintain stability or achieve desired objectives.
What is a Closed-Loop Control System Process?
In a closed-loop control system, the process involves continuously comparing the system’s output to a desired setpoint and using feedback to make adjustments to inputs or parameters to minimize any difference between the output and the setpoint.